With the continuous expansion of forklift applications, the demand for forklift parts in different industries and different usage scenarios presents the characteristics of diversity and complexity. Customers not only require reliable quality and performance, but also want to meet personalised and customised demands. For example, in the logistics and warehousing industry, the diversified demand for forklift attachments is high; and in some special working conditions, such as ports, mines, etc., the wear resistance and corrosion resistance of the parts are more demanding.
At present, forklift parts supply involves many links and participants, including parts manufacturers, distributors, maintenance service providers and so on. However, in the actual operation process, the information communication between the links is not smooth, and the co-operation is not close enough, resulting in the overall inefficiency of the supply chain. For example, parts inventory information is not transparent, easily resulting in inventory backlog or out-of-stock phenomenon; the distribution of maintenance parts is not timely, affecting the progress of equipment maintenance and normal use of customers.
Forklift aftermarket parts supply market is highly competitive, and some suppliers ignore the improvement of product quality and service level in order to pursue short-term interests. Some counterfeit and shoddy parts flow into the market, which not only bring safety hazards to forklift users, but also damage the reputation of the whole industry. In addition, the unregulated and unprofessional after-sales service also affects customers’ experience and satisfaction.
Strategies and measures to optimise and upgrade the supply of forklift truck parts and components
Establishing an efficient supply chain management system is the key to optimising parts supply. Forklift enterprises should play a central role in strengthening close cooperation with upstream and downstream enterprises such as parts manufacturers, distributors, maintenance service providers, etc., so as to achieve information sharing, resource integration and collaborative operation. Through the establishment of a unified information platform, they can grasp real-time information on parts inventory, demand and distribution, optimise the supply chain process and improve the responsiveness and flexibility of the supply chain. For example, the use of advanced Internet of Things (IoT) technology, parts and components for the whole traceability and management, to ensure the quality of parts and components and the timeliness of supply.
In order to improve the versatility and interchangeability of parts and reduce maintenance costs and inventory pressure, the forklift industry should vigorously promote the standardisation and modularisation of parts and components. Develop unified standards and specifications for parts and encourage parts manufacturers to produce according to the standards, so that different brands and models of forklift trucks can realise the compatibility and interchangeability of parts and components. At the same time, strengthen the modular design, divide the forklift into multiple functional modules, each module consists of standardised parts and components, which is convenient for maintenance and replacement, and improves the maintainability and reliability of the equipment.
Quality is the lifeline of parts supply. Parts and components manufacturers should increase investment in R&D, introduce advanced production processes and equipment, improve the level of production and manufacturing to ensure that the quality and performance of parts and components meet the requirements of high standards. Strengthen the construction of quality control system, from raw material procurement, production and processing to product testing, each link should be strictly controlled to prevent unqualified products into the market. At the same time, pay attention to the industry’s technological development dynamics, and actively research and develop new products and technologies, such as new energy forklift parts, intelligent control parts, etc., in order to meet the market demand for high-end, intelligent parts.
High-quality after-sales service is an important guarantee to optimise the supply of parts and components. Forklift enterprises should establish a sound after-sales service network and improve the coverage rate and service quality of service outlets. Strengthen the training and management of maintenance personnel, improve their professional skills and service awareness, and ensure that they can provide timely, efficient and professional maintenance services for customers. In addition, it should also provide diversified service content, such as regular maintenance, equipment testing, technical advice, etc., to meet the different needs of customers and enhance customer adhesion!
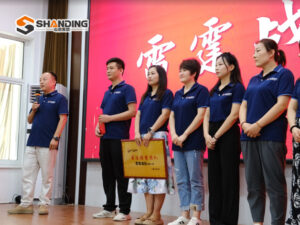
A shower of red envelopes, a “horse race” system, and team competitions—Shanding Group’s September 2025 Procurement Festival has begun, sparking a passionate and dynamic internal com